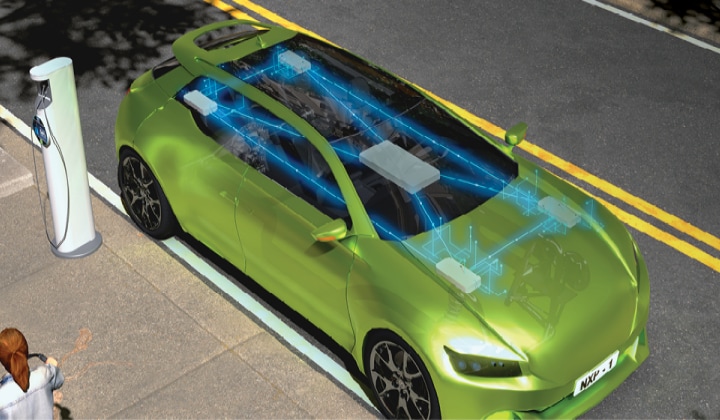
Different battery architectures have inherent advantages and disadvantages. Vehicle OEMs, need to analyze and decide which architecture is a better fit for their production models while keeping the system at a competitive price. One innovative solution for this challenge is to use two independent 400 V batteries.
The two 400 V batteries can be connected in series when charging (800 V in total), reducing the charging time and connected in parallel when driving (400 V). This enables the use of standard high-volume 400 V drivetrain components like the inverter and on-board-charger, where the capacity and range remain unaffected.
This approach can gives designers the best of both worlds by allowing fast charging and the reuse of existing 400 V solutions. Costs are controlled, but they there is the enormous competitive advantage of much faster charging, making their car more appealing to consumers.
This diagram above shows the key systems in an EV powertrain. You can see the main high voltage (HV) battery, with its management system. The low voltage (LV) battery is lead-acid or also lithium-ion based and delivers typically 12-14 V. This delivers the lower voltages required for systems such as interior lighting, door locks, navigation and driver assistance. The 12 V battery also provides a backup source of power to take over safety-critical functions such as steering, if the main HV battery cannot provide power.
For any solution, there are criteria that are non-negotiable, regardless of cost. The car must have inherent functional safety, and must meet all relevant safety and environmental regulations wherever it is going to be sold. In order to be a success, the vehicle also needs to offer features and benefits that consumers want, which means the car must have sufficient range, performance and comfort, as well as a style.
Firstly, they should look at the components on their bill of materials (BOM). Has this list been simplified where possible? Can any components be replaced with lower-cost, more integrated alternatives? Or will changing one component provide benefits elsewhere – such as a processor or system on chip (SoC) that reduces the number of external parts needed?
For example, the analog front end (AFE) is an essential part of the battery management system (BMS)—acquiring data from the battery cells and digitizing and conditioning the resultant data. By using a highly integrated AFE, such as NXP’s MC33775A, a 14-channel battery cell controller, the BOM cost can be reduced and overall system costs cut by decreasing the amount of cabling required.
Then, the designer can think about the production and manufacturing process. Can they select components that will enable automated assembly, bringing down costs?
Also, can cost savings be achieved with a modular design that’s reusable and scalable across multiple car models? This approach is common nowadays, with a single vehicle platform underpinning different body styles. This means that the car manufacturer can offer consumers multiple options without their development costs ballooning and can benefit from economies of scale in component costs. For example, Volkswagen has adopted NXP’s BMS into its MEB platform, making it much easier to scale this system across many car models – which is a big advantage, considering that VW is planning to bring up to 75 full EV models to the market by 20291.
Looking more specifically at the BMS, this will acquire data from the battery cells, and analyse it to determine the battery’s SoC and state of health (SoH). The BMS can use this data to manage the battery for optimal performance, range and lifetime, and can also diagnose any problems.
In this blog, we’ve examined how designers can keep costs down for an EV, specifically the component costs related to the BMS. While these general principles hold true for any EV, they may be particularly important when moving to an 800 V architecture, which is likely to have higher component costs and fewer alternative sources for parts.
To learn more download our whitepaper.
Emiliano Mediavilla Pons joined NXP in 2015 as Product definer and functional safety architect for Solid State Lighting business, coming from the Tier1 automotive sector. From 2018, Emiliano joined the BMS group as Principal Functional Safety Architect in the application team. For the last fourteen years, Emiliano has been working on the automotive sector as system, product and functional safety architect. Emiliano holds a Bachelor’s degree in Electronics Engineering from University of Oviedo, a Master’s degree in Automotive Electrical and Electronics from Polytechnic University of Catalunya and a Master’s degree in Business Administration (MBA) from University of Oviedo.
Konrad Lorentz holds a Bachelor’s Degree in International Project Engineering from Reutlingen University. He joined NXP through a thesis paper on the Automotive Value Chain in 2020 and now holds a position as Product Manager in the BMS Marketing Team.
June 21, 2022
May 25, 2022
May 9, 2022
by Davina Moore